Textiles and Clothing by Kate Heintz Watson (best free ebook reader txt) 📖
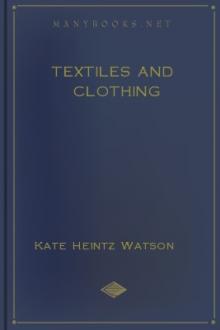
- Author: Kate Heintz Watson
- Performer: -
Book online «Textiles and Clothing by Kate Heintz Watson (best free ebook reader txt) 📖». Author Kate Heintz Watson
The silk of commerce begins with an egg no bigger than a mustard seed, out of which comes a diminutive caterpillar, which is kept in a frame and fed upon mulberry leaves. When the caterpillars are full grown, they climb upon twigs placed for them and begin to spin or make the cocoon. The silk comes from two little orifices in the head in the form of a glutinous gum which hardens into a fine elastic fiber. With a motion of the head somewhat like the figure eight, the silk worm throws this thread around the body from head to tail until at last it is entirely enveloped. The body grows smaller and the thread grows finer until at last it has spun out most of the substance of the body and the task is done.
If left to itself, when the time came, the moth would eat its way out of the cocoon and ruin the fiber. A few of the best cocoons are saved for a new supply of caterpillars; the remainder are baked at a low heat which destroys the worm but preserves the silk. This now becomes the cocoon of commerce.
Next the cocoons go to the reelers who wind the filaments into the silk yarn that makes the raw material of our mills. The cocoons are thrown into warm water mixed with soap in order to dissolve the gum. The outer or coarser covering is brushed off down to the real silk and the end of the thread found. Four or five cocoons are wound together, the sticky fibers clinging to each other as they pass through the various guides and are wound as a single thread on the reels. The silk is dried and tied into hanks or skeins. As the thread unwinds from the cocoon, it becomes smaller, so other threads must be added.
At the mill the raw silk goes to the "throwster" who twists the silk threads ready for the loom. These threads are of two kinds—"organize" or warp and "tram" or filling. The warp runs the long way of woven fabric or parallel with the selvage and it must be strong, elastic, and not easily parted by rubbing. To prepare the warp, two threads of raw silk are slightly twisted. Twist is always put into yarn of any kind to increase its strength. These threads are united and twisted together and this makes a strong thread capable of withstanding any reasonable strain in the loom and it will not roughen. For the woof or tram which is carried across the woven cloth on the shuttle, the thread should be as loose and fluffy as possible. Several threads are put together, subjected to only a very slight twist—just enough to hold the threads together so they will lie evenly in the finished fabric.
After the yarn leaves the spinners it is again run off on reels to be taken to the dye house. First the yarn is boiled off in soapy water to remove the remaining gum. Now the silk takes on its luster. Before it was dull like cotton. The silk is now finer and harder and is known as "souple."
The silk fiber has a remarkable property of absorbing certain metallic salts, still retaining much of its luster. This process is known as "loading" or "weighting," and gives increased body and weight to the silk. Silk without weighting is known as "pure dye," of which there is little made, as such goods take too much silk.
For the weighting of white or light colored silk goods, tin crystals (stanous chloride) are used and for dark shades and black, iron salts and tannin. By this means the original weight of the fiber may be increased three or four hundred per cent. This result is not attained, however, except through the weakening of the fiber.
Common salt has a very curious action on weighted silk. It slowly weakens the fiber. A silk dress may be ruined by being splashed with salt water at the seashore. Most often holes appear after a dress comes back from the cleaners; these he may not be to blame for, as salt is abundant in nearly all the bodily secretions,—tears, perspiration, urine.
Artificial silk is made by dissolving cellulose obtained from cotton. It is lacking in strength and water spoils all kinds manufactured at present.
Silk, like wool, has the property of absorbing considerable moisture without becoming perceptibly damp. Like wool and all the animal fibers, it is harmed by alkalis. The important physical properties of silk are its beautiful luster, strength, elasticity and the readiness with which it takes dyes. Silk combines well with other fibers, animal and vegetable.
A comparison of the relative value of textile fibers may be seen from the following approximate prices:
Cotton—$.07 to $.14 per pound; loss in cleaning and bleaching 5 per cent.
Flax—$.12 to $.30 per pound; loss in cleaning and bleaching about 20 per cent.
Wool—$.15 to $.30 per pound; loss in scouring 20 to 60 per cent.
Raw Silk—$7.00 to $10.00 per pound; loss in "boiling off" about 30 per cent which is made up and much more by "loading."
MODERN METHODSAll the complex processes and machinery of the textile industry are but developments of the old-time methods of the home. Brief outlines only will be given here for the processes are most intricate in detail.
SPINNINGThe spinning of cotton yarn (thread) is typical of all the fibers. The stages may be divided into—
2. Carding.
3. Combing.
4. Drawing.
5. Spinning.
The picking and carding have for their object the removal of all foreign substances with as little damage to the fiber as possible. The foreign substances in cotton are sand, dirt, pieces of leaves, seed, husk, etc., which have become mixed with the fiber during the process of growing, ginning and transportation.
The cotton bales are opened and thrown into the automatic feeder which carries up a layer of cotton on a spiked apron from which it is removed by a rapidly revolving "doffer" underneath which is a screen which catches some of the dirt. It is next fed between rolls in front of a rapidly revolving blunt-edged knife which throws out more of the dirt through a screen. There is a suction of air through the screen which helps remove the foreign substances. The cotton passes through several of such machines, being formed into a soft web or "lap" which is wound into a roll.
The carding machine further cleans the fibers and lays them in a general parallel position. From this machine the web is formed into "sliver," a loose rope of cotton fiber about two inches in diameter. This is received in circular cans.
The combing is omitted for short fiber cotton, but is used in worsted spinning and with long staple cotton to remove the short fibers. Cotton to be used for making yarn suitable for hosiery, underwear, sewing thread, lace, and for very fine cotton fabrics is carded.
In drawing, from six to sixteen "slivers" are run together and the fibers drawn out in several stages until the soft rope is about an eighth of an inch in diameter, called "roving." This tends to get rid of any unevenness and makes the fibers all parallel. From this machine the roving is wound on a bobbin ready for the spinning frame.
The spinning frame may have a hundred spindles or more, each one of which is drawing out its supply of "roving" to the required size of yarn and giving it the twist necessary to bind the fibers together. The yarn to be used for the warp is given a harder twist so that it may be strong enough to stand the strain in weaving. The yarn for filling is usually left soft.
The yarn for warp is now usually given a coating or "sizing" of starch and gums so that the thread may not become unwound and break during weaving.
The process of spinning is much the same for flax and for wool, although somewhat differently constructed machines must be used. Flax is usually spun wet.
WEAVINGThe modern power driven loom is a wonderful piece of machinery. The principle of its operation is essentially the same as the hand loom, but it is almost perfectly automatic in its action, a man or woman being able to tend from ten to fifteen looms weaving plain cotton goods.
The yarn coming from the spinning frame is sometimes dyed before weaving. The warp is formed by winding as many threads as the width of the fabric is to contain on a slowly revolving drum, called a "beam," in the same relative position in which they are to appear in the finished cloth. From its position on the beam at the back of the loom, each thread is brought through its particular loop or eye with the heddle, then passes through its own slot in the reed, and down to the roller or "cloth beam" that is to take up the woven cloth. This is called "drawing in the warp." If there is a piece of cloth coming from the loom, the work is very simple, for the ends of the new warp are tied to the ends remaining from the warp that has been woven out.
The shuttle with its bobbin, containing the yarn of the filling, is much the same as is used in the hand looms, except for form and size, which varies according to the requirements and size of the warp being used. At first only one shuttle was used, but in 1760 Robert Kay invented a mechanism by which several shuttles containing different grades or colors of yarn might be used. Each throw of the shuttle
Comments (0)